Making assumptions is a necessary part of diagnosing mechanical problems, and of living life in general. But like most things, there are good and bad assumptions. Good assumptions based on empirical evidence, factual information, experience and knowledge can be quite helpful. But bad assumptions, as Robert Pirsig reminds us in Zen and the Art of Motorcycle Maintenance, are traps to be avoided as they can mislead, direct you down dead-ends, and greatly complicate the task at hand.
I was reminded of the dangers of bad assumptions recently when I picked up a six-pack of Third Shift Amber Lager, assuming it was an award-winning craft beer from some new little brewery. Why did I make that assumption? Because Coors did a very good job of making it look like a little craft beer, and I did a poor job of being an informed consumer. I made the purchase based on the packaging and the point of sale pitch, not on factual information and knowledge, and the beer turned out to be a mediocre lager at best (although at 5.3% ABV it wasn't a total waste). Fool me once, shame on you.
You would think that this recent beer episode would have made me more wary of bad assumptions, but human nature is what it is, and I once again fell prey when I misdiagnosed a failing water pump on our 2002 Chrysler Town and Country as a power steering pump failure. It all started a few months ago when I noticed I was losing some power steering fluid and the steering system became a bit noisy. A little research indicated any number of possible issues, anything from a bad rack and pinion to a clogged filter screen in the fluid reservoir, which means I was now in a process of elimination. A visual inspection appeared to clear the reservoir filter screen as a possible issue. I next added some Lucas Power Steering Stop Leak, which is supposed to help recondition the seals in the steering system. Voila! The noise disappeared almost immediately, and a check of the fluid a few days later confirmed that the level was holding steady. I thought all was well, but a couple of weeks later the noise came back (bad assumption time, it was not the same noise thought it was very similar). Over time the noise became worse, progressing from a squeal to a squeal with a grind in the background. Given my focus on the steering system, I assumed at this point that the bearings in the power steering pump were going bad. An occasional small puddle of reddish fluid on the garage floor seemed to confirm this, since the Lucas product turned the power steering fluid from clear to red/orange. Of course, this was actually coolant leaking from the water pump weep hole and not power steering fluid; a simple taste test then would have saved me a lot of time, trouble and money.
Under normal circumstances, I would have installed a new PS pump right away, but our cash flow is pretty tight at the moment. So I took a wait and see approach, which was a mistake. Because after several weeks of waiting and seeing with no apparent change in the situation, I let Daughter the Younger use the van. Sure enough, while driving to Caribou with a friend this week, Daughter the Younger experienced her first automobile breakdown as a licensed driver when the water pump seal blew out, spewing chewed up bearings and antifreeze (the red/orange variety, not the green kind) all over, and throwing the serpentine belt off the various drive pulleys. When she called to tell me about it, she said the vehicle suddenly got very hard to steer and there was red liquid dripping out. This only served to further reinforce my bad assumption of a failing PS pump. With the wife and Daughter the Elder at work I was flat out of vehicles to go get her. Fortunately, her friend’s father was available to pick them up.
The next day I took the truck down to the local Sinclair station (these are real car guys, they slick back their hair with 10-W-30), gave them keys to the van, told them where it was and waited for them to tow it home. When it arrived, there was fluid all over the flatbed, way too much for it to be power steering fluid. A quick taste test confirmed it was antifreeze, and the cartoon lightbulb over my head was suddenly illuminated. Once the tow truck was gone, I slid under the van and grabbed the water pump pulley – loose as hell, wobbly as a drunken teenager. While I felt fairly dumb for walking right into the assumption trap I had set for myself, I tried to focus on the bright side. Installing a new water pump was going to be an easier, and cheaper, repair job than a PS pump (or, God forbid, a rack and pinion unit).
Now, on the transverse mounted 3.8 liter V6 engine in our van, there’s no way to accomplish this repair job from above – you have to go after it from the passenger-side wheel well. And it goes something like this…
First, disconnect the cable from the negative battery terminal. This is to prevent any potential damage to the electronics controlling the antilock brake system that could be caused by a short, or an accidental deployment of the airbags. Jack up the front of the vehicle, support it on jack stands, and remove the passenger-side wheel and splash guards. Now you have access to the water pump on the front of the engine block. I had done this once before a couple of years ago to replace the serpentine belt tensioner and idler pulley, so no big deal. Since the belt was already off the pulleys, it was easy to remove (though I knew it would be a bit of a pain to get back on). Next I disconnected the lower radiator hose to fully drain the cooling system. Before going any further, I took the Prizm to the auto parts store and picked up a new water pump, a tube of silicone gasket sealer, a gallon of antifreeze and just to be on the safe side, a new serpentine belt (the old one, only a couple of years old, now serves as a spare).
Back home, I crawled under the van to remove the old water pump. First step is to disconnect the pulley – easy peasy, just remove the three 13mm bolts holding the pulley to the three-pronged mount on the shaft. There’s not enough room betwixt water pump and frame to get the pulley all the way off at this point, you have to just work around it as you remove the five 10mm water pump mounting bolts. I got four off with no problem, but the fifth was a real bugger. Not enough room to get a ratchet and socket to that one, so I said screw it, ran to the hardware store and got a ratcheting box-end wrench. That did the trick. Now, with the mounting bolts removed, you have to really manipulate the pump and pulley to get them out. There’s not much room at all between the engine block and frame, it’s just a matter of trial and error, and a lot of patience, and as many swear words as the task deserves.
With the old water pump out, I scraped clean the mounting surface on the block with a putty knife and, just to be safe, cleaned it with some solvent until it was as smooth as Cary Grant. I then prepped the new water pump, applying a bead of silicone sealer to the gasket channel and putting on the gasket. This is a good time to take a short break as the silicone has to set up for about ten minutes, and you just know it’s going to be a royal bitch getting the new pump through that zero-clearance opening between block and frame. From there, as the manuals like to say, installation is reverse of removal. Take the water pump and pulley and wiggle, wriggle, finagle and finesse (but do not force) them back into mounting position. Take care not to damage the exposed impeller blades or pull off the gasket. Then you reinstall the five mounting bolts. The manual says to torque them to specs, but you pretty much have to rely on feel to get the tightness right because I don’t see any way of getting a torque wrench onto at least two of the five bolts. Reinstall the pulley on the pump and you’re ready to put the serpentine belt back on. This can be a potentially dangerous procedure since you have to compress the spring-loaded tensioner to get the belt over the last of several drive pulleys (crankshaft, power steering pump, water pump, alternator, air conditioning compressor, idler and tensioner). I do the AC compressor pulley last as it’s the easiest to reach while compressing the tensioner from underneath the vehicle. While you can accomplish this job with an adjustable crescent wrench applied to a square lug on the end of the tensioner, I find it easier to borrow a serpentine belt tool from the auto parts store. It’s basically a flat metal bar with a socket drive on one end that fits into a square hole in the tensioner. It’s less prone to slip off under tension and gives you much better leverage.
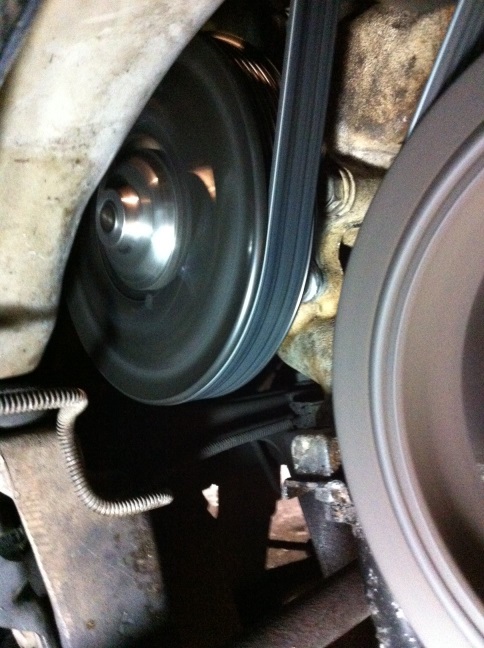
With the belt back on I reconnected the lower radiator hose and filled the system with coolant. At this point you fire up the engine and let it warm to operating temperature (i.e. until the thermostat opens to fully circulate the coolant through the system – be sure to turn on the heater so the heater core doesn’t get left out). Top off the coolant in the radiator and make sure the overflow reservoir is full as well. Then put on the radiator cap to pressurize the whole system and check the new water pump to make sure there are no leaks. Shut off the engine and reinstall the splash guards. These are held on by a combination of sheet metal screws and plastic connector pins. You almost always break at least one or more of those pins in the removal process, but they only cost about a buck each. Reuse any that you can and replace those you break with new ones. Then put the wheel back on, tighten the lug nuts to specs, lower the vehicle and you are good to go.
Happy driving, citizens!
Or, since i didn't have time to go get new ones, you can replace those plastic connectors with my favorite: cable ties!
Any port in a storm, eh?
Darn tootin'. The use of cable ties is even worse on the skid plate for my Golf. That plastic just doesn't hold up.
Since I just had 2 water pumps replaced, this felt like an extremely pertinent read. But mostly, I just wanted to say that you're a hell of a writer Twayn. I read parts of this aloud to my wife. Simply beautiful.
Car repair pr0n. Good stuff, Twayn.